Is it better to have lift in a station or no lift?
This is a question that is often debated in planning and design reviews. Engineers may argue that it helps give access for automation to better move the panels from station to station and helps maintain integrity in trim stations keeping the tooling stronger. Maintenance personnel may counter that saying it adds more moving parts that wear and have to be replaced (wear plates, cylinders, pins & bushings, etc.) causing more expense through the life of the tool. Additionally someone may bring up needing lift to break the burr or lube adhesion and another will point out it reduces stability of the panel at pick up or drop off. These are all valid points and the truth is, there isn't a simple "one size fits all" answer to the question. Let's look at a few examples of when lift makes sense and when it doesn't.
Pro's (To Lift...)
- Lift allows access for grippers / shovels without needing to cut pockets into trim or form steels.
- Lift in a station can reduce the total amount of transfer lift required (if part characteristics allow & lifters are positioned properly) and increase overlap between lift and pitch axis.
Con's (Not to Lift...)
- More moving components increasing the complexity initial build cost
- Will require more maintenance over the lift of the tooling.
- Lift can raise the overall panel height in the tool and make restrictive chokepoints tighter reducing the available transfer time for the panel
Example #1 (To Lift)
Many of us have seen designs that look similar to the images below. While this condition can be acceptable if you are trimming thin material, cutting the new higher strength steels or thicker material may lead to failure with clearance pockets too close to trim edges. Additionally, trim lines can get altered after the build begins as blank development is refined or engineering changes come into play. This can lead to scrapping and replacing a trim steel which is both costly and time consuming.
By using lift in a situation like this, the trim steel is much stronger and any trim line modifications would have little impact on the viability of the steel.
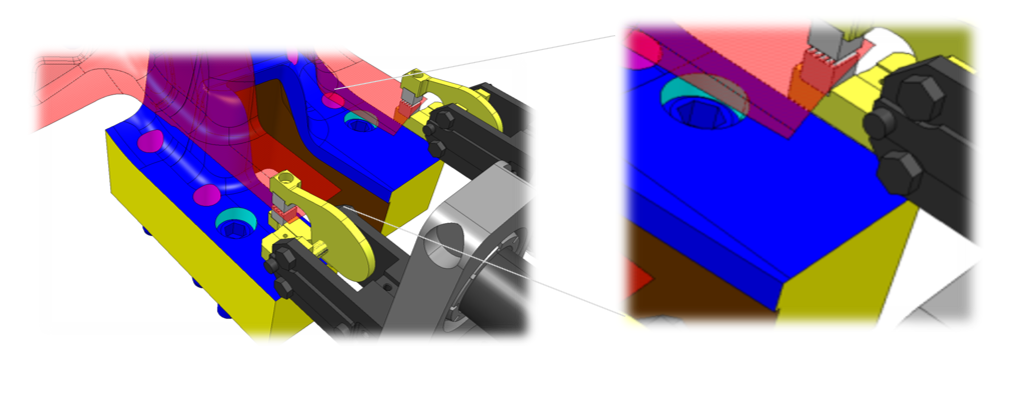
The previous example is visually straightforward, but a more nuanced and often overlooked factor can provide an even stronger reason to incorporate lift in this scenario. By allowing space for overlapping clamp and lift motions, production throughput can be significantly enhanced. Many engineers underestimate the impact of motion overlap on cycle time, yet even a small overlap in non-linear motion profiles used by transfer systems can yield substantial time savings.
Sufficient lift in a station creates an opportunity to share more time between corresponding axis, optimizing the transfer cycle for greater efficiency. While overlapping with a pocket remains an option, it always involves balancing the trim wall's strength against the pocket's depth. A deeper pocket creates a weaker trim wall so its understandable why they try to keep it as shallow as possible.
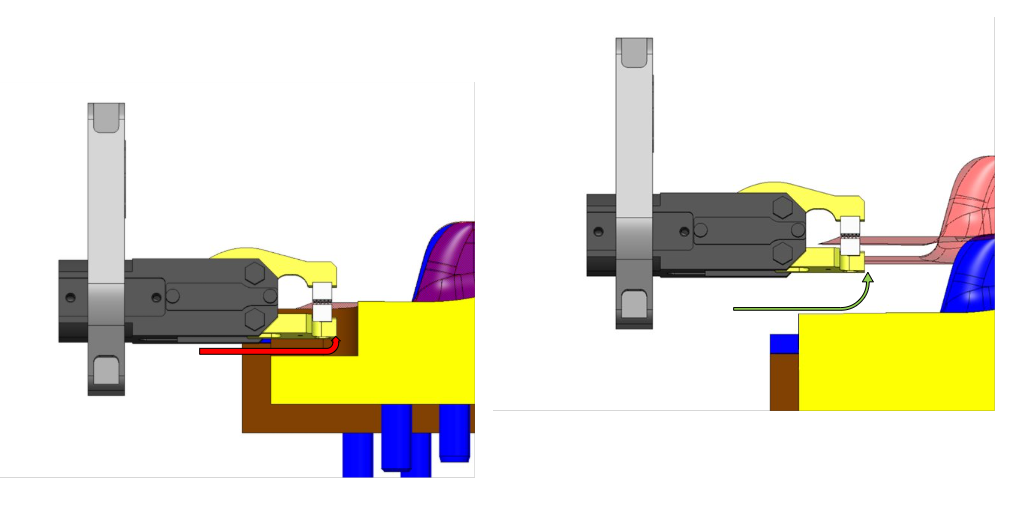
To give an example of just how much overlap can impact SPM, we will look at a typical 15spm transfer recipe with no overlap on clamp and lift.
By simply adding 3mm of overlapping distance to the clamp to lift motion
and 6mm of overlapping distance to the lower to unclamp motion
with a re-optimized curve, we can achieve an increase of +2spm (from 15-17spm) while running all the movement speeds exactly the same and maintaining the same clearances to the upper and lower tooling throughout the cycle!
In this example, lift not only improves the strength of the lower trim steel, it can increase the production throughput by +2spm or more! This increase would more than pay for the extra components and maintenance cost over the life of the tool.
Example #2 (Not to Lift)
This one is simple enough for anyone to grasp... even without full understanding of designing for production. If there is no potential gain in SPM, no loss of integrity from pocketing, and no improvement in access for automation, there is no benefit to adding lift!
In the example above, there is plenty of room under the gripper to add overlap the the trim steel is plenty thick to have sufficient strength for trimming.
Incorporating lift into the station in this example would lead to increased component purchases, additional machining, and ongoing maintenance throughout the tool’s lifespan. With a typical lifter assembly build up utilizing guided keepers (or similar products), nitrogen cylinders, springs, and potentially extra safety spools would significantly raise the initial cost of building and machining the station. Depending on the complexity of the setup and lift requirements, this cost could range from approximately $2,000 USD on the lower end to $5,000 USD or more. In an industry largely driven by cost, this could be the difference between a build shop winning a package and losing it.
Example #3 (To Lift)
Some parts have very long vertical "legs" or down flanges that require a significant amount of lift for the part to clear the lower post or other tooling obstructions (cams, heels, etc.) before pitch forward can begin. In situations like these, adding lift can really improve the smoothness of the transfer curve.
In the example below, the lift up to pitch forward chokepoint is a push-pull form cam that requires 120mm of lift straight up before Pitch forward can begin.
By lowering the station 50mm and adding 50mm of lift in the lower post, the pitch forward movement can begin much sooner providing better part control by reducing the g-forces on the part and transfer and allowing more cycle time to move the panel from station to station.
This will be reflected in the lift up, lift down, and the pitch forward motions with more than a 10% reduction in acceleration for each axis while maintaining the same production rate.
Example #4 (Not to Lift)
This example gets a little deeper into looking at all the potential impacts of adding lift. To this point, we've only looked at the impact of adding lift as it relates to the lower tooling but, we can't forget to consider what impact adding lift has in the upper tooling.
In some cases, adding lift can result in less time to transfer the panel from station to station. Continuing to play off the previous example, adding lift would require us to lower the working height of the station (so we can maintain the incoming / outgoing part height) If this station had a pad in the upper, it would also have to be "lowered" in the (Z) axis to have the proper finished working height when the die was closed.
If that pad was the tightest point between the upper die and the automation, then doing this could effectively move the clamp in and / or clamp out choke points down the press curve resulting in the transfer having to wait longer to clamp in (as the upper comes up out of the way) and require the transfer to extract the automation out of the die space sooner to avoid the upper pad as the press is closing. In this case, the part control gains achieved by lowering the station are negated by the loss of available time.
The Bottom Line
Every project is unique, and certain circumstances may determine whether incorporating lift is beneficial. The key is to thoroughly evaluate the potential impacts before initiating tooling design. While tight project timelines often create pressure to move quickly, rushing through the planning phase without considering production implications can significantly affect a project's success—both at launch and throughout its lifespan.