Rotating Parts from station to station
At T-SIM, we work with hundreds of stampers and one thing that is a common challenge is tipping parts from station to station. Most stampers will try to utilize a drop-tip to accomplish rotation as simply as possible. While this does have its advantages, it can often cause many unnecessary problems as well. When a drop-tip is used, you are temporarily losing control of the panel during the cycle. The challenge with this is that as you run higher speeds, even a very short loss of control can be catastrophic. If the panel gaging is not sufficient or you are tipping too much, you can encounter sensor faults (increasing downtime), miss-hits, and there is even the possibility of damaging your automation or tooling significantly.
Because of this some have looked for other alternatives like using an on-the-bar rotary actuator to rotate the panel as it is transferring from one station to the next. Unfortunately many who have tried this option consistently complain that they have all kinds of problems with them. While these can be very challenging to use, they are also a very valuable tool that can help you better process and produce a metal stamped part. With proper understanding, there is no need to fear using on-the-bar rotators in your transfer tooling.
The Problem
On-the-bar rotators can be very complex and challenging to setup in the press. Add to that many hands involved in making adjustments over the course of a production lifecycle and these very useful tools can become a source of frustration for many stamping facilities. The infinite number of locations for the gripper and automation build up off the rotator seems too much to be able to have a simple solution... Don't lose heart once you understand a couple basic principles of these tools, you'll be able to set and reset your rotators in just minutes!
Basic Principles
On-the-bar rotators being utilized in a tri-axis press line rely on a couple basic principles... the first is that it is ALWAYS the centerline of the rotators rotation axis that determines where the part will land... and where the gripper is placed on the panel has NOTHING to do with where the part will land! This is often the hardest part for many to understand. We can assure you it is true and will prove itself out if you follow the steps we outline below for your next rotator project.
The second principle is that the rotator on the front bar must be perfectly in-line with the one on the back bar for it to function properly. In the past, we suggested using laser bore sites to achieve this alignment but, have since come up with simple and more efficient methods.
The Solution
So how do you make setting on-the-bar rotators simple? As with most things, it starts with planning. We suggest you add to your standards that any job that utilizes rotators has the following requirements detailed out.
- The centerline axis of rotation must be confirmed in planning phase of tool design. To confirm the axis is correct, make sure it is straight and level in (Z) from front to back of the press, and you should be able to take the part in the station, rotate it the desired degrees about the axis, and pitch it down equal to the transfer pitch value and have it land in the next station perfectly. If you prefer a slight drop above the station, make sure that is accomplished with the location of the rotation axis.
- In the station where the panel is picked up, there should be a raised boss on the outside edge of the casting (approx. 100mm wide in the flow direction and 50mm deep toward the centerline). This boss should be centered right to left on the rotation axis line and have a machined step in-line with the rotation axis. *If you are using a "Plate Style die shoe", simply weld or dowel a block to the top surface of the shoe to act as a boss.
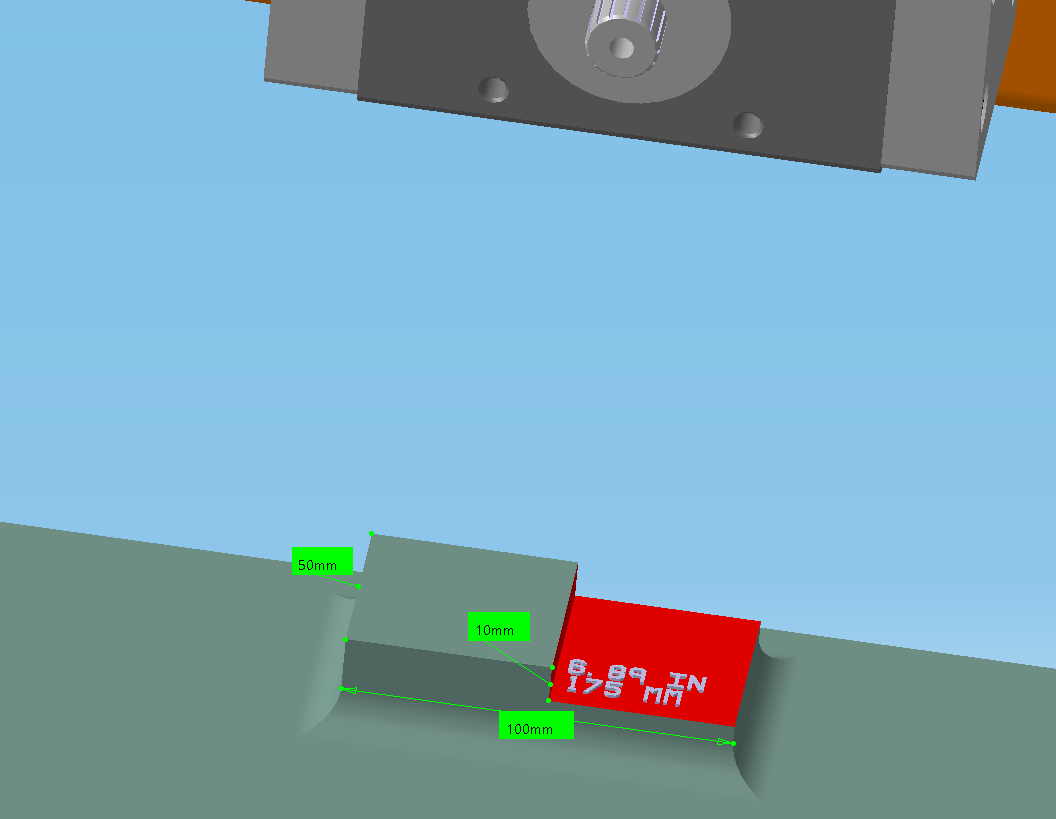
- The machined height of the boss should be a nominal distance (it makes it easier to set that way!) from the rotation axis in the (Z) direction (this can be in either inch or metric depending on company unit preference). The distance should be stamped or etch-machined into the machined surface of the boss.
- Make sure that both the front and rear of the die have the same bosses with the heights clearly marked and in line so front to rear alignment can be achieved.
- To set the rotator, you can rough mount it to the transfer bar (be sure your design has adjustability designed into it) and move the transfer bar in so the shaft of the rotator is at or near the edge of the castings / lower shoe.
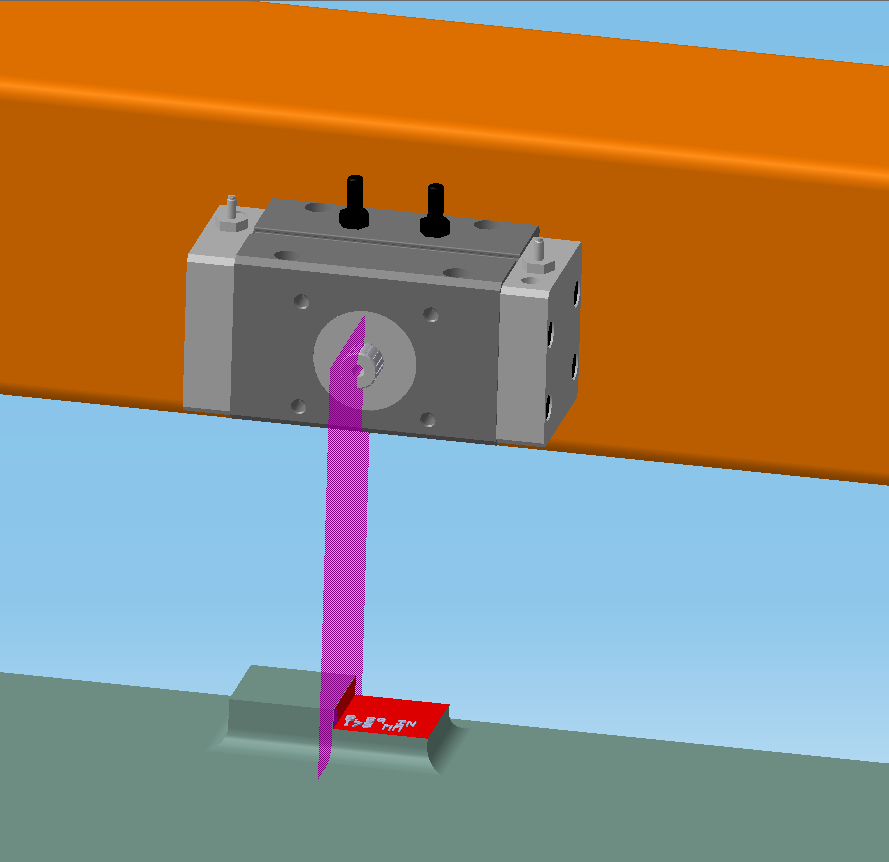
- Next place a machinist square flat on the machined surface of the boss and bump it up to the machined centerline of the rotation axis. Mark the height on the vertical edge of the square (if it does not already have measurements indicated on it)
- Adjust the rotator to align with the edge of the square at the marked height and securely tighten all mounting screws to "lock-in" the location.
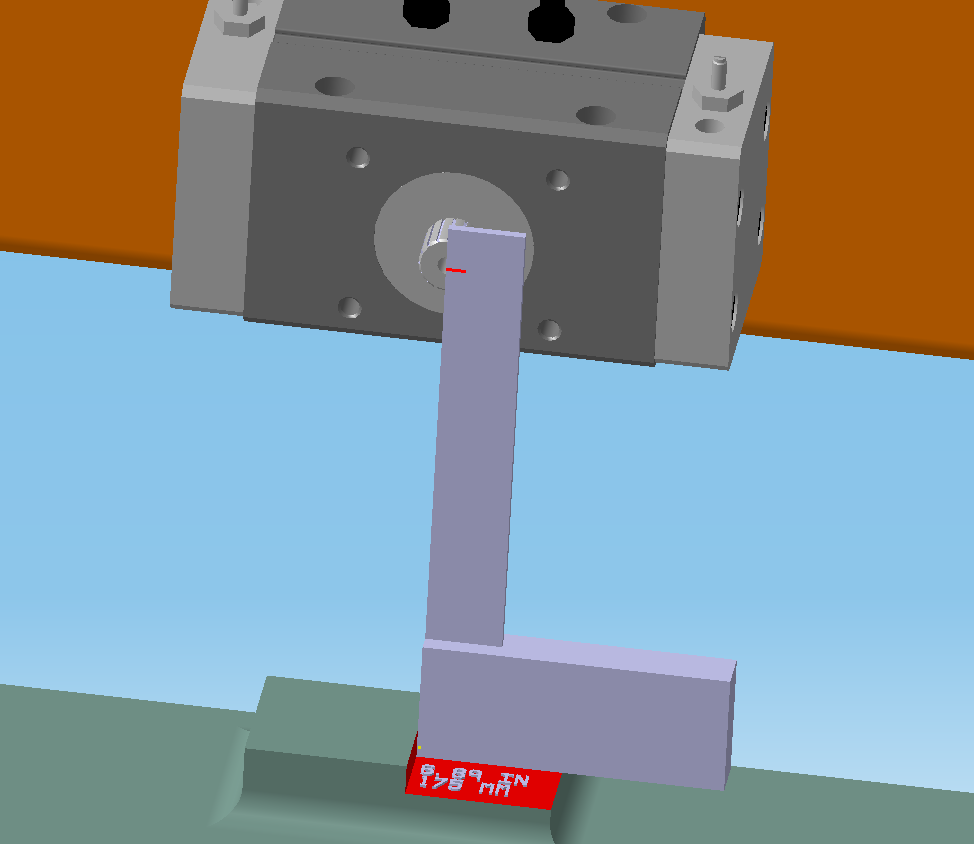
- Repeat the process for the rear rotator (if you have automation on both front and rear bars).
- Finally, attach your automation to the rotator face and make certain when you set the grippers / shovels that they are not relocating the panel at clamp in stop when the grippers close. Sometimes an improperly set gripper can move the panel in (Z) or a misplaced finger / shovel can move the panel in (Z) or left to right.
- Confirm that the panel transfers well and located properly at drop off. Once you are happy with the rotation, you can tack-weld any mounting to make it semi-permanent and dissuade modifications by well-intention operators, or simply mark clearly on any mounting brackets the "home" position so it can be moved back in the event of a crash or improper adjustment.
Some final thoughts...
If your panel does not properly locate after following the above steps, review the design and make sure the axis is properly positioned to locate the panel in the drop off station (as described in step #1 above), and double-check that you measured properly up from the machined surface. If all that shows correctly, confirm that the machined centerline edge on the boss is properly located (measuring from another know location like a pin or a key slot is the best way to confirm this).
Be sure to use a "flow control" valve on the airlines to your rotator if it does not already have a way to control the speed of rotation. These inexpensive units can be the difference between success and frustration when using rotators.
By following these simple steps you'll make the headaches of using rotators a thing of the past! Best of all, should someone crash or improperly adjust the rotator during a production run, it will be a piece of cake to set it back the the correct original location when using this method.
Happy Rotator Setting!!!
Related Articles
When does T-SIM make changes to Automation, Travel Distances or Design?
Why Would T-SIM’s Service Department Make Changes? While we aim to avoid modifications, our priority is to ensure the highest possible strokes per minute (SPM), confirm that suppliers adhere to customer standards, and verify that the automation being ...
CAD Data FAQ
CAD Data FAQ When do we send the CAD data to T-SIM service department? When to send the data depends on what service(s) the T-SIM service department is providing for you. RFQ Data: T-SIM can quote new tooling simulation using: just a detailed 2D or ...
New Tooling Deliverables and How to Use Them
T-SIM Service Department Transfer Die Simulation Deliverables for New Tooling General Information we provide back: Corrective Action Reports Also known as CAR's, are the deliverable we create from the results of the simulation. The CAR's are ...
Recommended Clearances using T-SIM software
There are a lot of factors to consider when choosing specific clearances for simulation and optimization. Equipment conditions (transfer slop, gripper air systems, press braking, etc.), controller capabilities, automation, die design, die conditions, ...
Welcome to T-SIM Simulation Services
Welcome Welcome to T-SIM's Simulation Service Department! Whether you are submitting a new tooling design for simulation, optimizing an existing tool, or requesting rechecks, we’re here to make the process smooth and efficient. Data With a wide ...